What supply chain leaders must learn from the baby formula shortage
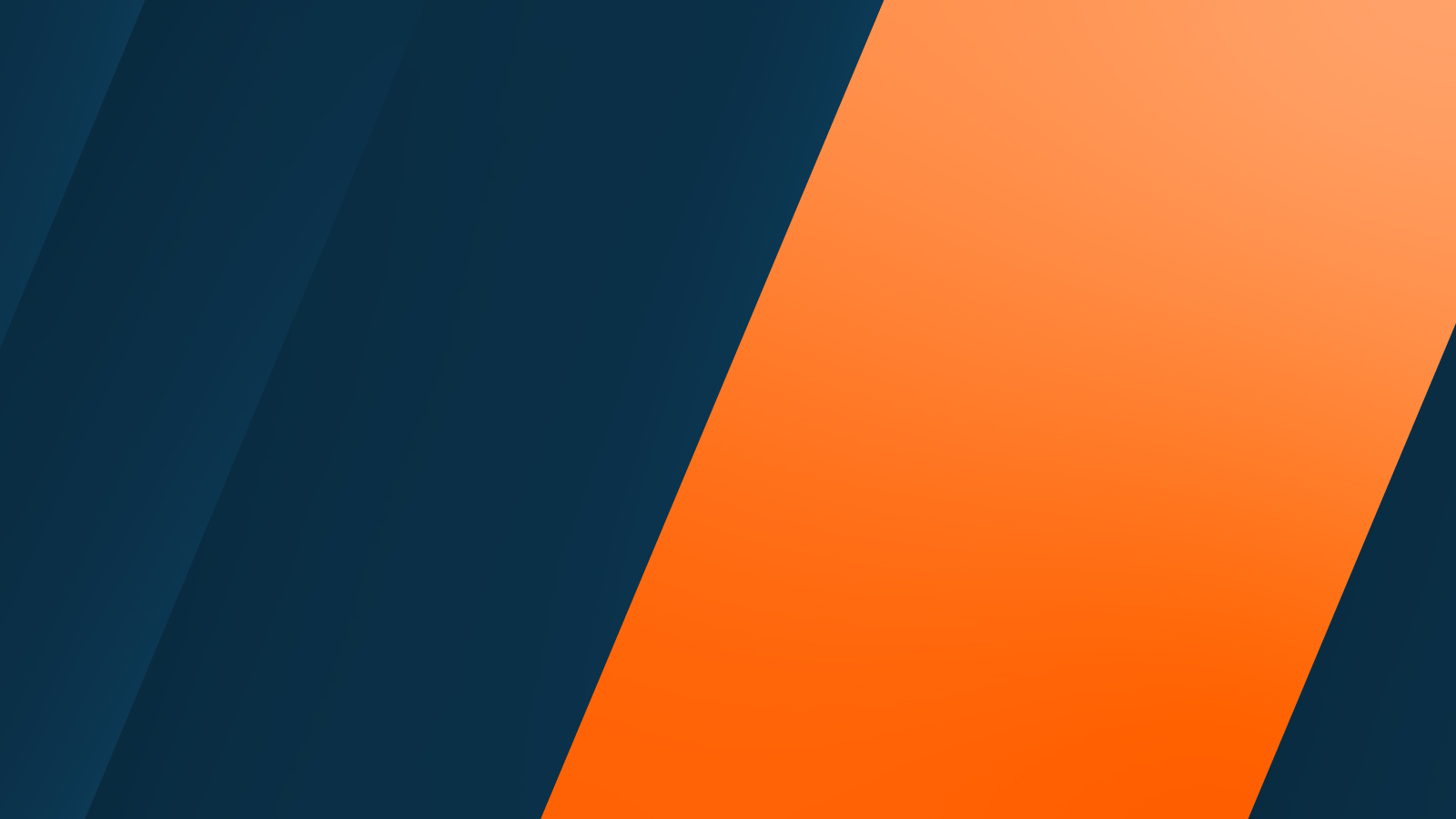
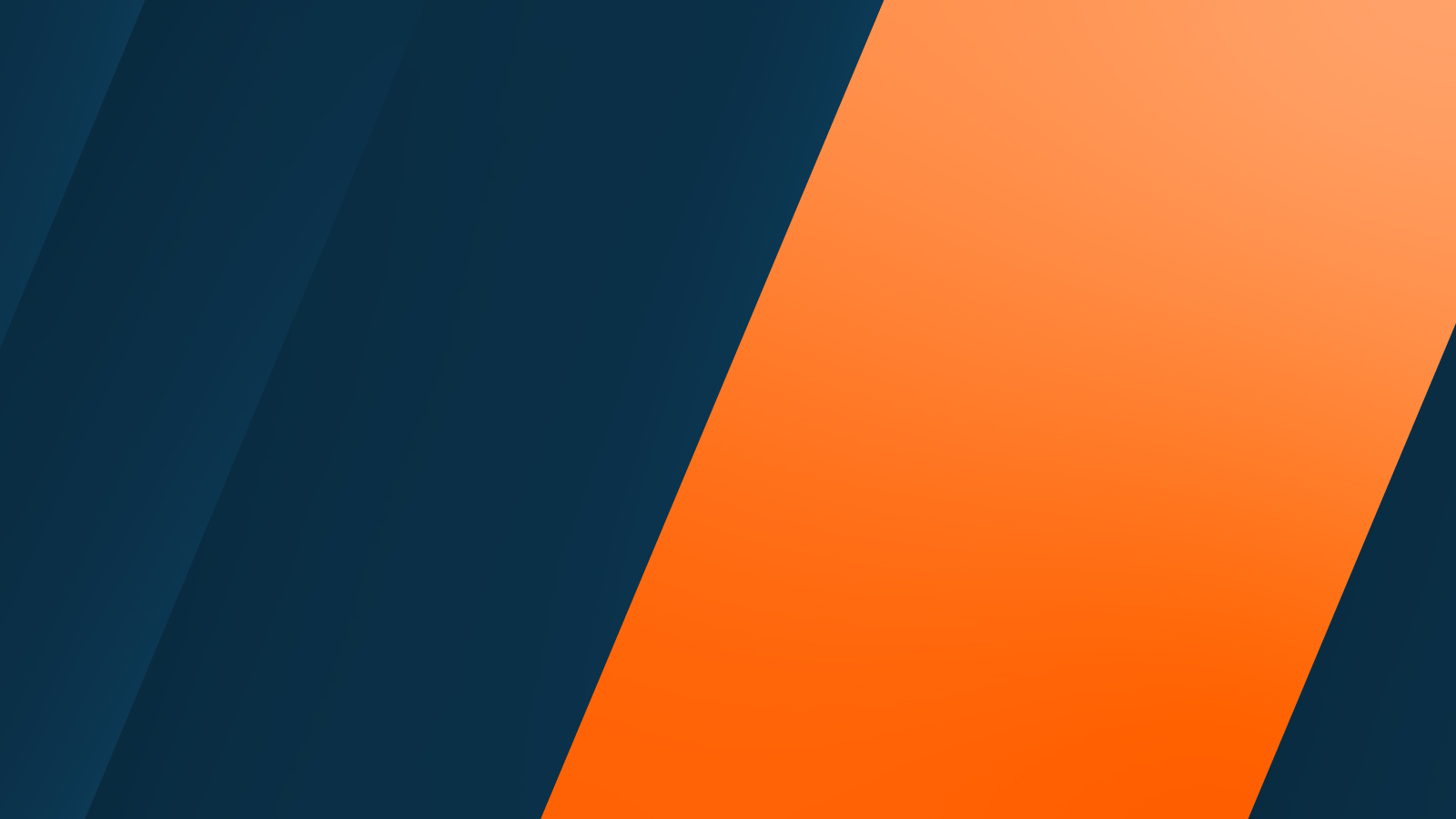
Lessons supply chain leaders must learn from the baby formula shortage.
A chaotic 2020, packed with unprecedented disruptions, dramatic climate events, and the first major global healthcare crisis in a century, rocked supply chains everywhere. Consumer awareness of the supply chain and how it impacts our communities and daily lives erupted virtually overnight. First came toilet paper, paper towels, and cleaning supply shortages, then semiconductors, rubber, and now, baby formula. Although all these shortages and gaps in the supply chain have come at a cost – accelerating already problematic inflation rates across the globe – for many, the domestic formula shortage is life-threatening.
The supply chain’s human impact
Haley Hodge shared with the Wall Street Journal podcast, The Journal, about the first time she walked down the baby food aisle at her local grocery store. Striding to the baby formula shelf with her newborn was a first she knew she would never forget, but not for the reasons she imagined.
“I thought to myself, wow, this is the first time I’ve ever been in the baby food aisle to actually buy baby items. Then I got there, and there was nothing on the shelf, and I thought, is this normal?” she recalled. “This was now a life-threatening situation because babies can’t not eat.” Finally, after zigzagging across her city from store to store, Hodge and her husband found enough formula for five feedings. She’s enlisted the help of her friends across Facebook to buy or alert her of formula sightings. But of course, that’s not enough, and every day is a challenge.
Her son, born six months premature, only eats formula. Hodge remembers going store to store, sitting in a parking lot at midnight with him in the backseat, crying, “He’s ready for his next bottle,” she said. “And we don’t have anything. Where are we going to go next to look? That was the most terrifying moment.”
It’s a moment that parents and family members across the U.S. live almost daily. This situation is dangerous for premature babies who need the high-caloric formula to live. Baby formula shortages can also mean life or death for kids with metabolic issues or even young adults with brain disorders.
According to The Wall Street Journal, formula is out of stock at 50% of retail locations in nearly half of the country. As the catastrophe reached a fever pitch this summer, the Biden administration authorized the Defense Production Act to increase formula supply. Meanwhile, they are easing import rules and looking to Ireland, Mexico, and the Netherlands, where only a handful of distributors can meet the United States’ rigorous formula standards. Baby formula is one of the country’s most tightly regulated food products – a contributing factor to the domestic industry concentration.
A formula for catastrophe
What started this supply crisis? One of the United States’ two primary formula providers, Abbott, had a problem. After two infants died and four others were sickened by a bacterial infection connected to Abbott’s formula, the Food and Drug Administration mandated a recall and opened an investigation into the formula producer in February 2021. Abbott was forced to shut down the source of the batches in question: its largest factory. That Abbott plant alone accounts for 40% of the U.S. baby formula supply. Just recently, the plant reopened. “We will ramp production as quickly as we can while meeting all requirements,” Abbott said.
For logistics and supply chain management leaders, this disruption is a powerful reminder of the human consequences of visibility into supply chain planning and management. Here are four takeaways that supply chain leaders should learn from the formula shortage.
- Own end-to-end supply chain visibility.
Recalls are part of business, and healthcare is no exception. Just this past April, Moderna recalled a Spikevax lot in Europe. The batch included 764,900 doses deployed across Norway, Poland, Portugal, Spain, and Sweden in January. After Moderna pinpointed a “foreign body” in one vial of the batch, the company acted.In June, consumers were urged to cook frozen fruit after Listeria findings.
To arm businesses, customers, and communities against disruption, supply chain leaders need to empower deeper visibility across every node of the chain. With end-to-end visibility, you can quickly track a bad batch’s origin and limit its impact to avoid an all-out-product recall, or, as in the case of Abbott, a total factory shutdown.
- Raise red flags around market concentration.
High market concentration leaves little room for building an escape route and finding alternative suppliers. The baby formula shortage is an alarming example of how market concentration can quickly escalate supply chain issues into dire health and economic concerns. Although the ongoing pandemic has stoked supply chain disruptions for two years now, part of the formula crisis stems back decades, to 1972 with the launch of a federal program to feed infants: the Special Supplemental Nutritional Program for Women, Infants, and Children, or WIC. WIC has amassed more than half of the nation’s formula market and its structure has enabled formula monopolies to dominate the United States.According to one economics professor, these WIC-generated monopolies have made it almost impossible for new brands to break into the formula market. Even a minor market player needs WIC contracts. “One plant has a really big impact on the industry,” South Dakota State University economics professor David Davis explained to Bloomberg. “This whole situation calls for a reexamination of how the formula market works.”
- Protect your brand reputation and consumer trust levels.
Supply chain, once in the background, is now splashed across social feeds and news headlines daily. More than ever, consumers have a high-level but meaningful understanding of how goods arrive at their doorsteps or grocery store aisles. When shortages or prices surge because a significant supplier goes MIA, the reputational damage is hard to shake.JBS, the largest meat supplier globally, is a prime example. After being hit by a cyberattack last year, the giant had to shut down all its U.S., Canadian, and Australian beef plants and ultimately paid $11M in ransomware fees. This kind of media blitz erodes brand trust and credibility, even – and especially – when market dominance is in play. News commentators discussed the company’s missteps while consumers balked at the price of meat.
- Focus on agile planning and replanning.
The ability to plan and replan – running “what-if” scenarios for unforeseen changes and disruptions in an intelligent and agile way – is critical to avoiding preventable shortages and significant business fallout. Being able to change plans in a purposeful way with insights across your business is fundamental to a resilient business and supply chain.
Avoid shortages and be ready to re-strategize
Ignite agile supply chain planning and end-to-end visibility with Anaplan, a Leader in the Gartner® Magic Quadrant™ for Supply Chain Solutions. Deliver accuracy, manage by exception with visibility across distributors, suppliers, and production facilities, and run “what-if” scenarios on the fly so a fresh plan is always ready. Learn more about Anaplan for Supply Planning.