November 14, 2022
2 min read
Godiva Japan adopts Anaplan for integrated supply chain data management
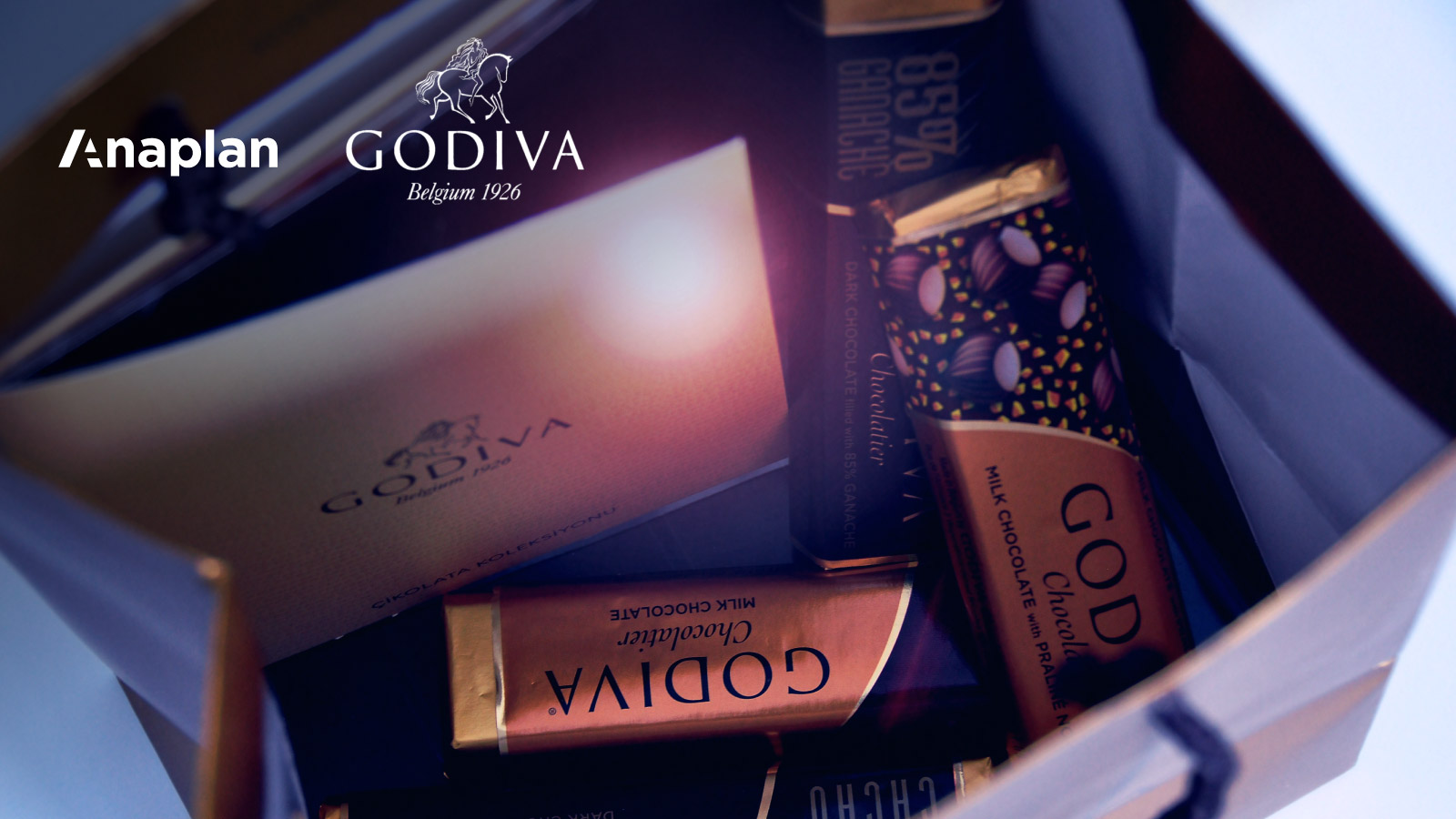
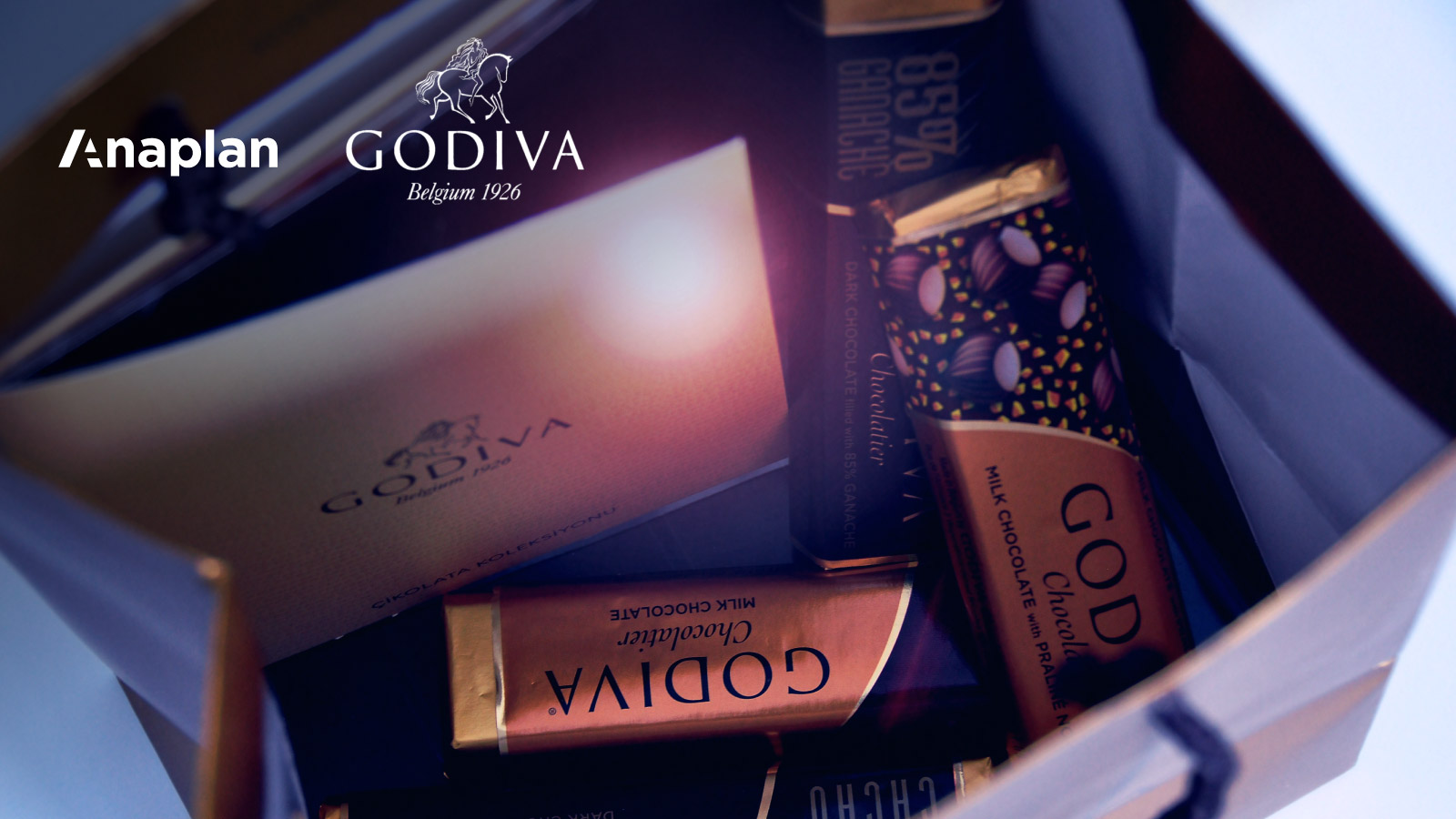
As part of premium global chocolate brand, Godiva Japan opened its first store in Japan in 1972. The company currently operates approximately 320 stores in the country, mainly in department stores and shopping malls, as well as seven “GODIVA café” stores in the Tokyo metropolitan area under the theme of “Elevating My Everyday.” Godiva has been growing its business by diversifying its sales channels in recent years, even during the COVID-19 pandemic. An incredible number of products meant as many as 10,000 items to contend with as part of the master data in the ERP system and it became increasingly difficult to accurately analyze sales and inventory status.
To build an optimal supply chain environment, Godiva embarked on a “Supply Chain Improvement Project” in three phases: Supply Planning, Sales and Operations Planning (S&OP), and Demand Planning. Upon review of current processes, it became clear that collecting data for S&OP from each department was overly complicated and burdensome where the complex and intricate spreadsheet data had to be analyzed and reported separately across departments. To alleviate this problem, Godiva Japan kicked off a project to adopt Anaplan in July 2021 and started full-scale operations in February 2022.
Once fully operational, Godiva Japan’s supply chain management has become significantly more efficient by linking sales, inventory, and POS data imported by the ERP system with Anaplan, enabling real-time information sharing without having to relay spreadsheet data among staff members. Monthly reports for S&OP, which used to take two people three days to prepare, are now expected to save approximately 300 hours per year.
In addition to saving labor in analysis and reporting, Anaplan has also increased the speed of decision-making in supply planning, preventing lost sales opportunities and excess inventory. Previously, the information necessary for management decisions was scattered throughout the company. After implementing Anaplan, the data was presented clearly and organized in the database, leading to a simplified planning process.
“Godiva’s mission is ‘We create Memorable Occasions of Happiness,'” said Mr. Shinya Kushiyama, Director, Supply Chain, IT and Product Operations, Godiva Japan. “We are focusing on omnichannel expansion to fulfill this mission by delivering ‘Memorable Occasions of Happiness’ to our customers as soon as they desire them. Anaplan has made great progress in our Supply Chain Improvement Project, and now we will be fully engaged in Phase 3, Demand Planning. In the future, we will use Anaplan to place orders with our Belgian factories and subcontractors and integrate it with our finance system to achieve even more efficient supply chain management.”
Anaplan Japan will continue to support Godiva Japan’s demand planning and contribute to its growth as a partner in achieving efficient supply chain management.