How to build a connected supply chain
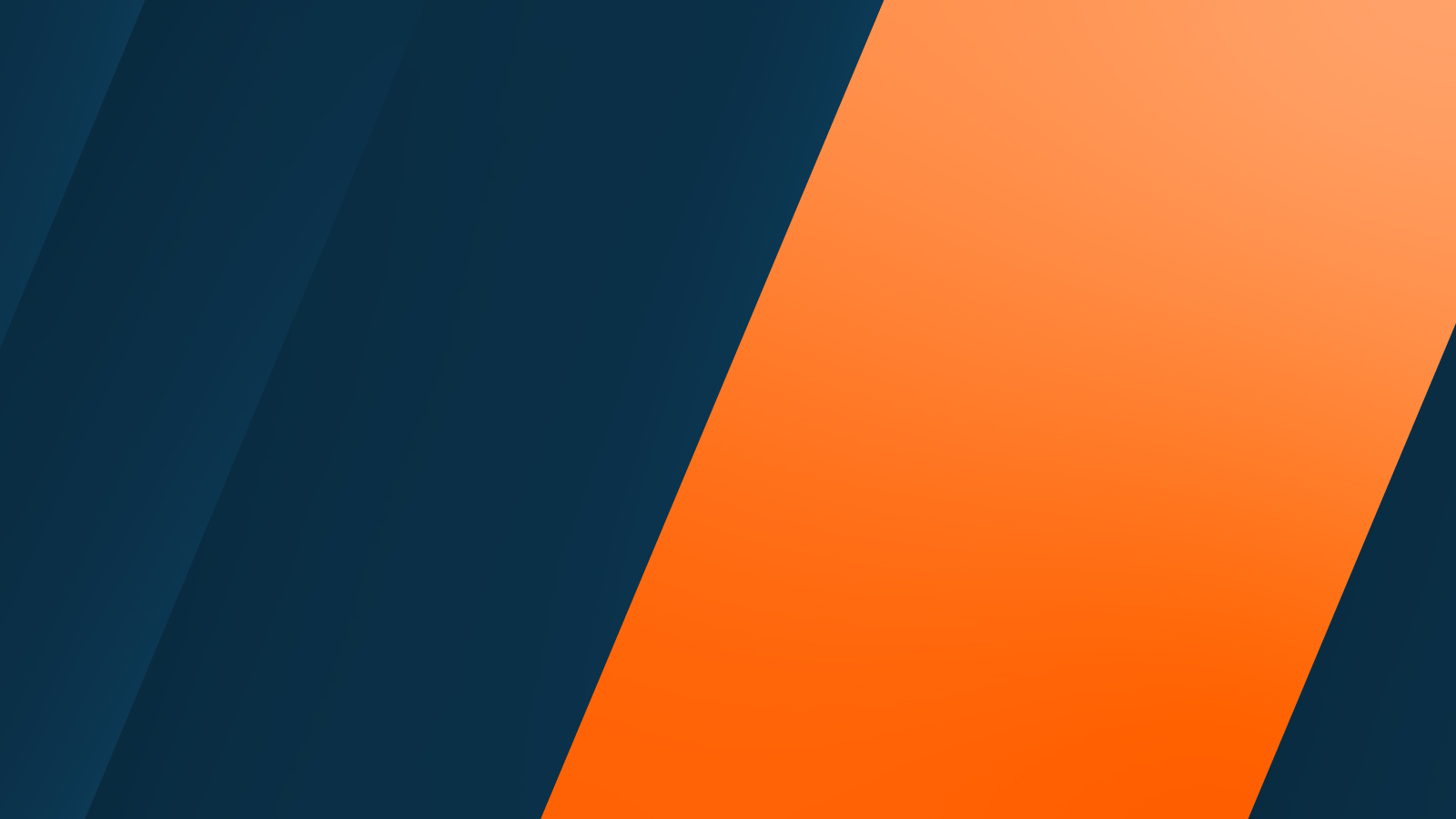
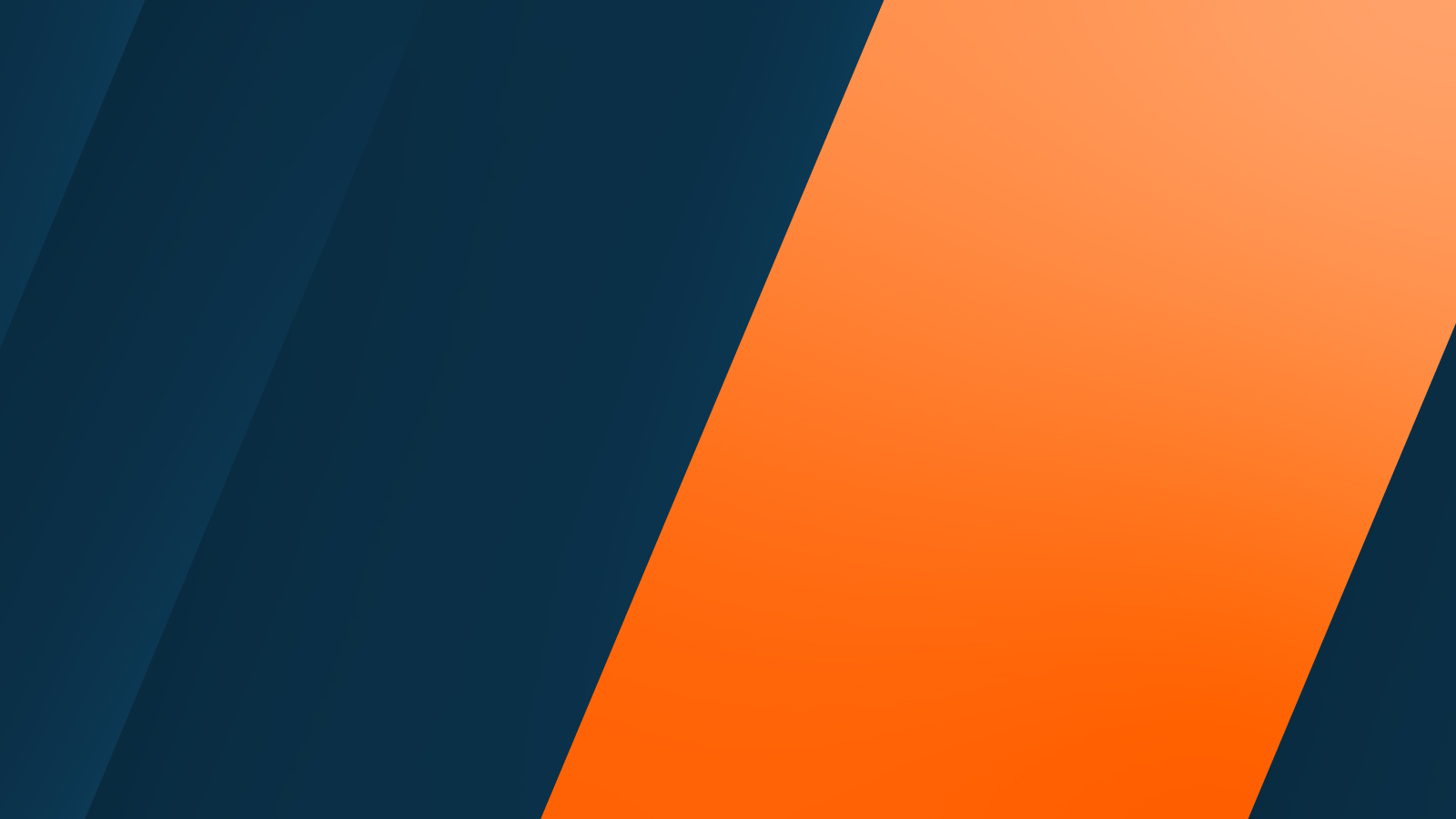
Supply chain management has undergone large-scale transformation in the past few years. In the past, companies primarily used enterprise resource planning (ERP) systems for collaboration and data tracking across the entire business. Today, some companies do their planning with a mix of spreadsheets and ERP systems, and others use cloud-based planning platforms. But this soon becomes messy, disjointed, and disconnected. Soon, this approach raises more questions than it answers.
- Are forecast numbers updated and shared across the business with relevant stakeholders, including sales, finance, and operations?
- Are inventory numbers from previous versions of a spreadsheet accurately entered into a new one?
- What do you do when disruptions like natural disasters and labor issues strike the supply chain?
Without connection, these questions go unanswered. And with the waves of change sweeping across the supply chain management world, you can’t afford to move forward with slow, siloed supply chain planning system. First, let’s define supply chain management, then we’ll talk about a few key areas of supply chain transformation, and finally, five tips for building connected supply chain planning.
What is the supply chain planning process?
Supply chain planning is the process of planning a product from raw material to the consumer. It includes supply planning, production planning, demand planning, and sales and operations planning.
- Supply planning determines how best to fulfill the requirements created from the demand plan. The objective is to balance supply and demand in a manner that achieves the financial and service objectives of the enterprise.
- Production planning addresses the production and manufacturing modules within a company. It considers the resource allocation of employees, materials, and of production capacity.
- Demand planning is the process of forecasting demand to make sure products can be reliably delivered. Effective demand planning can improve the accuracy of revenue forecasts, align inventory levels with peaks and troughs in demand, and enhance profitability for a particular channel or product.
- Sales and operations planning (S&OP) is a monthly integrated business management process that empowers leadership to focus on key supply chain drivers, including sales, marketing, demand management, production, inventory management, and new product introduction.
The digital supply chain revolution is already here
At the Gartner Supply Chain Executive Conference in London, Marc Engel Global, Chief Supply Chain Officer at Unilever, shared this reminder: “Innovation is not about machines; it’s about asking ‘what do people want?’” For supply chain professionals, those people are consumers. To effectively serve their needs, supply chain systems innovation must focus on the needs of the consumer.
A key challenge in the supply chain digital revolution is “people transformation.” It’s key to unlearn the old rules and define the new rules. It means saying “we’ll only do things that will have customer impact, not just for efficiency’s sake.” Mike Burkett presented Gartner’s point of view, which emphasizes that digital transformation is more than just digital optimization. Digital supply chain transformation focuses on building new business models.
How to achieve connected supply chain planning
To succeed in a growing global market, you must adapt effectively to the digital revolution and seek out practical ways to connect your supply chain planning from start to finish. Here are five steps we recommend to achieve connected supply chain planning.
- Make the move to real-time supply chain planning
When using ERP systems and spreadsheets for planning, companies typically rely only on historical data, resulting in little wiggle room for changes should any disruptions occur in demand or supply. For example, based on the previous year’s numbers, a company can estimate the number of products it will sell in the next quarter. But what if a massive hurricane destroyed a key distribution center, leading to too little supply on the shelves? With Anaplan’s real-time connected supply chain management solution, you can create “what-if” scenarios and plan more effectively so you’re ready when disruptions occur. - Unify supply chain planning with enterprise planning
A vital second step is connecting traditionally siloed supply chain planning to sales and operations planning and financial planning. Companies can benefit from synchronizing their short-term operational planning with their wider business planning processes to make real-time updates to inventory forecasts and supply. Deploying real-time S&OP solutions that enable enterprise-wide collaboration means key stakeholders across the business can create new scenarios and quickly assess how to use their resources wisely to optimize profitability when an unforeseen event happens. - Anticipate the demand of the end customer
For consumer-packaged goods companies, anticipating what customers want and when they want it is an ongoing challenge. A solution like Anaplan allows end-to-end visibility across the supply chain, and beyond their existing network of wholesalers and retailers to sense demand signals from customers. When you can rapidly identify changing consumer sentiments and assess how that changes demand for your product, it benefits your company, partners, and customers by improving profitability, margins, and lead time. - Leverage real-time data across all points of the supply chain
Because supply chain planning typically involves a myriad of suppliers, channels, customers, and pricing schemes, models soon become large and potentially unwieldy—especially when spreadsheets are your primary planning tools. Incorporating a solution that uses real-time data allows you to plan with more accuracy and reduces the risk of stock-outs or having too much inventory. - Ensure you have the flexibility to cope with change
When you have technology that lets you plan efficiently and react quickly, disruptions aren’t disruptive because re-planning and re-forecasting is easy—resulting in time and money saved and increased profitability.
Disruptive technology is the new normal
Emerging technologies like blockchain, artificial intelligence, and machine learning are generating massive amounts of hype and attention in the supply chain management world. It can be difficult to find your way through the hype, but as they’re becoming ubiquitous, supply chain planners need to understand how to harness them for maximum benefit.
For example, blockchain can be used in supply chain management for smart contracts, for maintaining ethics and sustainability, and for better security, traceability, and efficiency. If you can effectively integrate this emerging technology into your supply chain, the sky’s the limit.
A new supply chain planner for a new supply chain
Along with new technologies and practices comes the need for a supply chain leader with a new set of skills. To lead the way into a transformative future, they need to combine technical and business knowledge with collaboration and communication skills. The ability to influence department leaders that partner with supply chain is key, as well as the skills to interact intelligently with leaders across the organization is essential, because supply chain initiatives often reach across business units. And strong business acumen is a must-have—you’ll be more effective working with your counterparts in finance, sales, and marketing if you can speak their lingo.
The effective supply chain leader of tomorrow is tech-savvy and comfortable working alongside the world of “machines.” Some have said that artificial intelligence won’t replace managers, but managers who work with AI will replace managers who don’t. This highlights the transformation taking place in supply chain: humanity is essential, but so is technology. And this leader is a storyteller—digging into the countless layers of the supply chain to find the issues and weaving the right story together to help solve them.
Are you ready to take your supply chain beyond its limitations driven by outdated ERP systems and spreadsheets? By effectively adapting to the supply chain digital revolution and following the steps to connected supply chain planning above, you’ll be ready to collaborate across the enterprise, quickly adjust to market changes, and reap benefits, including lower costs and increased efficiency.