April 28, 2022
3 min read
What the railway strike crisis reveals about operational readiness
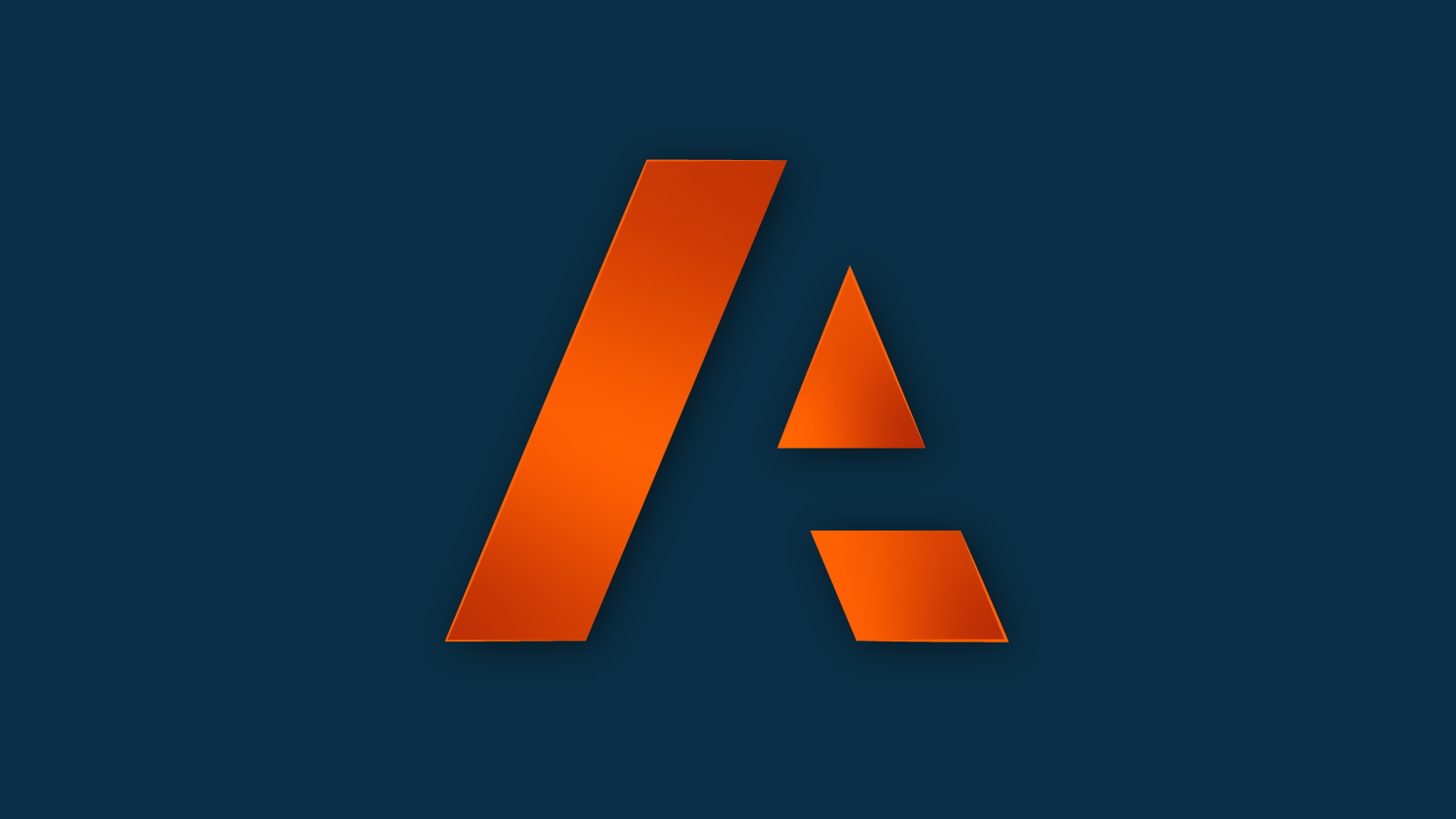
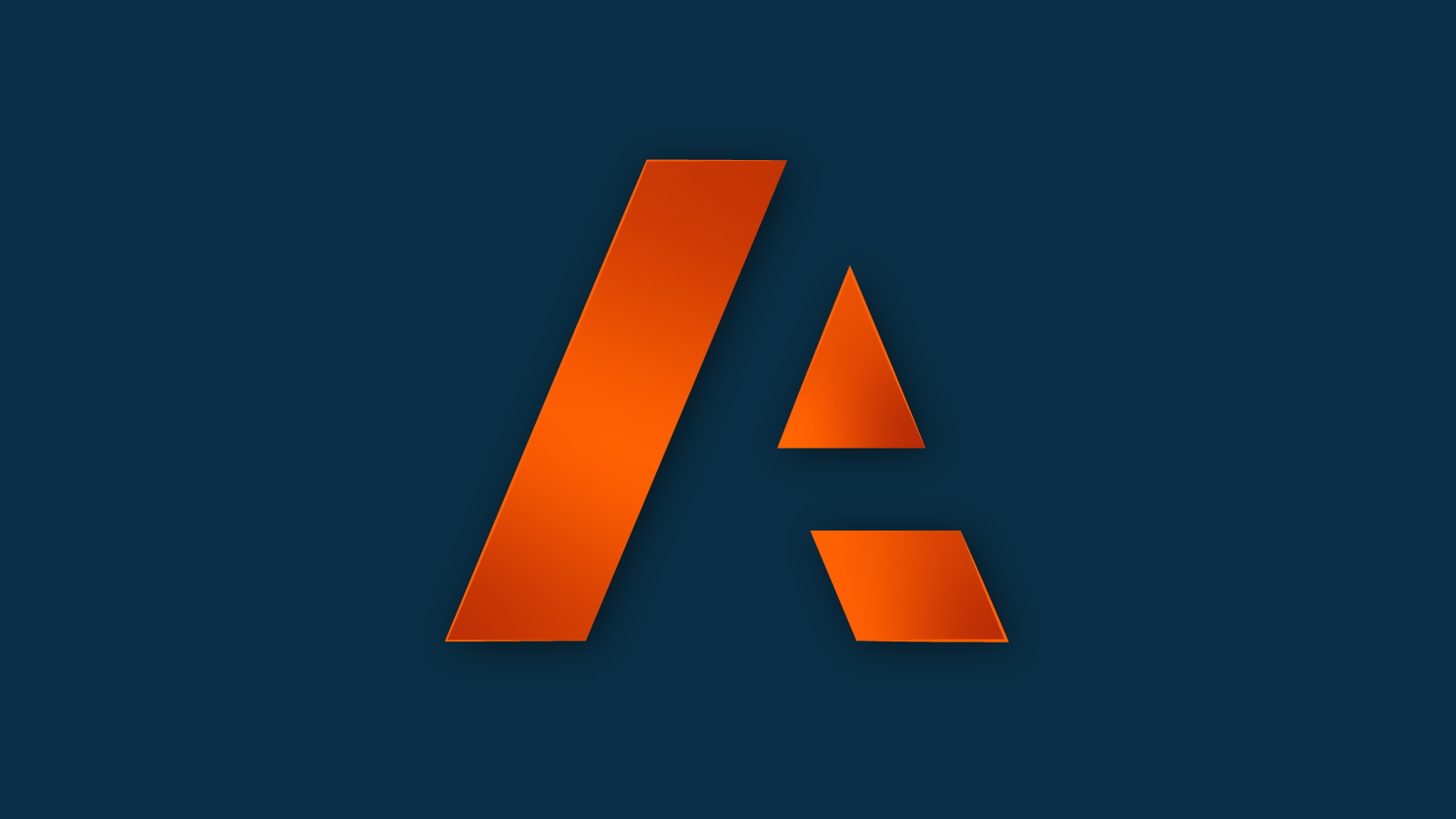
By Tom McDonough, Supply Chain Solutions Marketing Director, with contributions from Kouros Behzad, Workforce Solutions Marketing Director
The railway strike that threatened to cost the U.S. economy over two-billion dollars per day is one that had been simmering for the last several years. Tight delivery deadlines and demands for increased efficiency combined to create grueling schedules and poor working conditions. These were just a few of the crisis indicators that were evident to anyone who wanted to see them. However, as long as businesses maintained profitability, there was little incentive to address the labor issues central to this dispute. A tentative agreement is holding off the strike for now.
This crisis is the result of shifting attitudes toward work, expectations for quality of life, a persistent demand for growth, and what some describe as an industry jostling for political power. A Connected Planning approach can help with all but the last of those pressure points. A business that continues to operate without fully integrated planning tools is flying blind. Agility, adaptability and operational readiness mean having the ability to connect people, data, and processes in a way that optimizes business – no matter the crisis.
How to strike-proof your business
There are five key components to crisis mitigation and management, and each is integrated into the Anaplan approach to Connected Planning.
1. Plan
Collaborative development and execution of plans increase awareness of risks and help to assign ownership and development of alternatives. A strike may seem to be sudden to the general public but the root causes simmer for months or years. Preparing and communicating plans that include alternatives with business partners, and within business operations, ensures that all parties are ready for what comes.
2. Address
The ability to map out multiple “what-if” scenarios and their potential outcomes in real time is critical. Visualizing a problem and its impact across the entire business enterprise deepens understanding. In the case of the rail workers, the industry tried to deal with a workforce issue as if it were solely a compensation issue. Connected Planning might have shown that increased pay did not necessarily decrease attrition under current conditions.
3. Explore.
What are the alternatives? This is a question that must be always front of mind when addressing supply chain issues. For example, if rail workers were to strike, shutting down the Port of Los Angeles, would it be possible to direct shipments to the Port of Oakland? Are there enough dock workers, trucks, and drivers? How do these decisions affect profit?
4. Adjust.
Persistently monitor actual to plan. The ability to monitor progress and adjust rapidly, continuously, and systematically is an absolute necessity in today’s business environment. Connected Planning tools that allow the areas of Finance, Workforce, Supply Chain, Sales, and Marketing to strategize collaboratively are best.
5. Learn.
Lessons that are not learned are bound to be repeated. Although data can inform decision-making, it’s up to business leaders to use it in a way that builds resiliency across the organization. Read this case study to understand how Queensland Rail used Connected Planning to address workforce strategy and innovation issues.
As of this writing, U.S. rail workers have yet to ratify the tentative agreement negotiated in Washington D.C. on September 15, 2022. It took a presidential intervention to avert this crisis, however, there are more effective, dynamic, and scalable ways to help businesses develop and execute long-range planning solutions. Anaplan leverages data to address operational risks long before they become actual threats.
Click here to get a demo of Anaplan’s Connected Planning solutions.